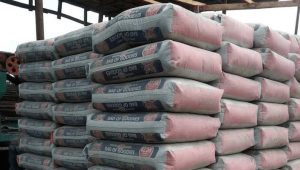
- The cement price in Nigeria has remained unstable over the years, driven by economic, infrastructural, and market-specific factors.
Nigeria’s cement price instability is a complex issue influenced by local and global economic factors, infrastructural deficits, government policies, and market dynamics.
Addressing these challenges requires a holistic approach, including improving infrastructure, fostering competition, stabilizing the exchange rate, and implementing policies to balance production and demand.
Without these interventions, the cost of cement is likely to remain unpredictable, posing challenges to Nigeria’s construction and real estate sectors.
Below are the key reasons contributing to the fluctuation in cement prices:
1. High Production Costs
The production of cement involves significant energy consumption and access to raw materials such as limestone.
Energy Costs: The erratic supply of electricity forces cement manufacturers to rely heavily on diesel and gas generators, which significantly increase production costs.
Raw Material Availability: While Nigeria is rich in limestone, the costs associated with mining, transportation, and processing are high due to inadequate infrastructure and security challenges in some regions.
2. Limited Competition
A few major players, such as Dangote Cement, BUA Cement, and Lafarge dominate the Nigerian cement industry. This oligopoly limits competition, allowing these companies to set prices with minimal external pressure. Additionally:
The entry barriers for new players are high due to the capital-intensive nature of the industry.
Import restrictions further reduce competition, giving domestic manufacturers control over pricing.
3. Logistics and Transportation Challenges
Transportation of cement from production plants to markets across Nigeria adds to the cost:
Poor Road Infrastructure: Bad roads lead to delays, increased fuel consumption, and higher maintenance costs for transport vehicles, all of which are passed on to consumers.
Insecurity: Insecurity in some regions, particularly in the North, increases the risk of transporting goods, leading to higher insurance and logistical costs.
4. Exchange Rate Volatility
Cement production relies on imported machinery, spare parts, and sometimes raw materials. The volatility of the Nigerian naira against major foreign currencies, particularly the US dollar, increases the cost of these imports. Manufacturers often adjust cement prices to offset the impact of currency devaluation.
5. Demand-Supply Imbalance
The demand for cement in Nigeria is high due to rapid urbanization, population growth, and government infrastructure projects. However:
Domestic production often struggles to meet this demand, leading to periodic shortages.
Seasonal factors, such as increased construction activities during the dry season, can also spike demand, causing temporary price surges.
6. Government Policies and Taxes
Government policies, such as import restrictions and tariffs, play a significant role in the price of cement:
Import Restrictions: The government has restricted the importation of cement to encourage local production. While this policy supports local manufacturers, it reduces supply, contributing to higher prices.
Taxes and Levies: High taxes on cement producers are often passed on to consumers, further driving up prices.
7. Market Speculation and Hoarding
Market speculation by distributors and retailers contributes to price instability:
Hoarding: When distributors anticipate price increases, they often hoard cement to create artificial scarcity, driving up prices.
Speculation: Rumors of government policy changes or supply disruptions often lead to panic buying, which further destabilizes the market.
8. Infrastructure Deficiencies
Nigeria’s inadequate infrastructure hampers efficient production and distribution:
Port Congestion: Imported production inputs often face delays at Nigerian ports due to congestion and bureaucratic bottlenecks.
Storage Facilities: Limited storage capacity for raw materials and finished products can lead to supply shortages, especially during periods of high demand.
9. Impact of Global Economic Trends
Global trends, such as the COVID-19 pandemic and the Russia-Ukraine conflict, have disrupted supply chains and increased the cost of production inputs like gypsum and coal, which are sometimes imported. These global factors have a cascading effect on cement prices in Nigeria.
10. Security Challenges
Ongoing security challenges, including banditry and insurgency in certain regions, affect the entire supply chain:
Mining operations in certain areas are disrupted, limiting raw material availability.
Distribution routes become unsafe, increasing costs for manufacturers and distributors.
Here are the prices of major producers of cement this week:
Price Of Dangote Cement
The current price of Dangote cement stands at ₦9,400 per 50kg bag, depending on the location.
Price Of BUA Cement
The retail price of BUA cement in Nigeria sells for ₦7,700
Price Of POP Cement
Pop White Cement or Plaster Cement – ₦9,700
Price Of Lafarge Cement
Lafarge Waterproof Cement – ₦8,900
Water Shield High Quality Waterproof Cement – ₦12,000
The post Price Of Bag Of Dangote, BUA, Other Cement This Week appeared first on Naija News.